Quality assurance is crucial when it comes to 5 gallon cap moulds, as precision is essential for consistent and reliable performance. Here are some key aspects of quality assurance that ensure precision with 5 gallon cap moulds:
Mould design and manufacturing: Quality assurance begins with the design and manufacturing of the moulds. Experienced mould designers and manufacturers use advanced software and technologies to create precise and accurate mould designs. They consider factors such as material flow, cooling efficiency, and part ejection to optimize the mould's performance. High-quality materials and precision machining techniques are employed to ensure the moulds meet the required tolerances and specifications.
Material selection: The choice of materials for 5 gallon cap moulds is critical to achieving precision and durability. High-quality, durable materials with excellent dimensional stability and wear resistance are selected. This ensures that the moulds can withstand the stress and pressure of the injection molding process without warping or deforming. The materials are also chosen to withstand the specific requirements of cap production, such as exposure to chemicals, temperature variations, and mechanical stress.
Testing and validation: To ensure precision, 5 gallon cap mould manufacturers undergo rigorous testing and validation processes. This includes conducting dimensional measurements and verifying that the mould produces caps that meet the required specifications. Functional tests are also performed to assess factors such as cap closure tightness, tamper resistance, and compatibility with cap sealing equipment. These tests help identify any issues and ensure that the moulds produce consistently high-quality caps.
Regular maintenance and calibration: Proper maintenance and calibration of 5 gallon cap moulds are essential to maintain precision over time. Moulds should be regularly inspected for wear, damage, or signs of degradation. Any necessary repairs or replacements should be carried out promptly to prevent issues that could affect the precision of cap production. Regular calibration ensures that the moulds maintain the desired dimensions and tolerances, optimizing the quality and consistency of the caps.
Process control and monitoring: Quality assurance extends to the injection molding process itself. Process control techniques, such as statistical process control (SPC), are employed to monitor and maintain consistent production parameters, such as temperature, pressure, and cycle times. This helps ensure that each cap produced with the mould meets the required specifications and maintains the desired precision.
Continuous improvement: Quality assurance is an ongoing process, and continuous improvement is crucial for maintaining precision with 5 gallon cap moulds. Feedback from production, customer input, and internal analysis is used to identify areas for improvement and optimize the mould design, manufacturing processes, and quality control measures. This commitment to continuous improvement helps enhance precision, efficiency, and overall product quality.
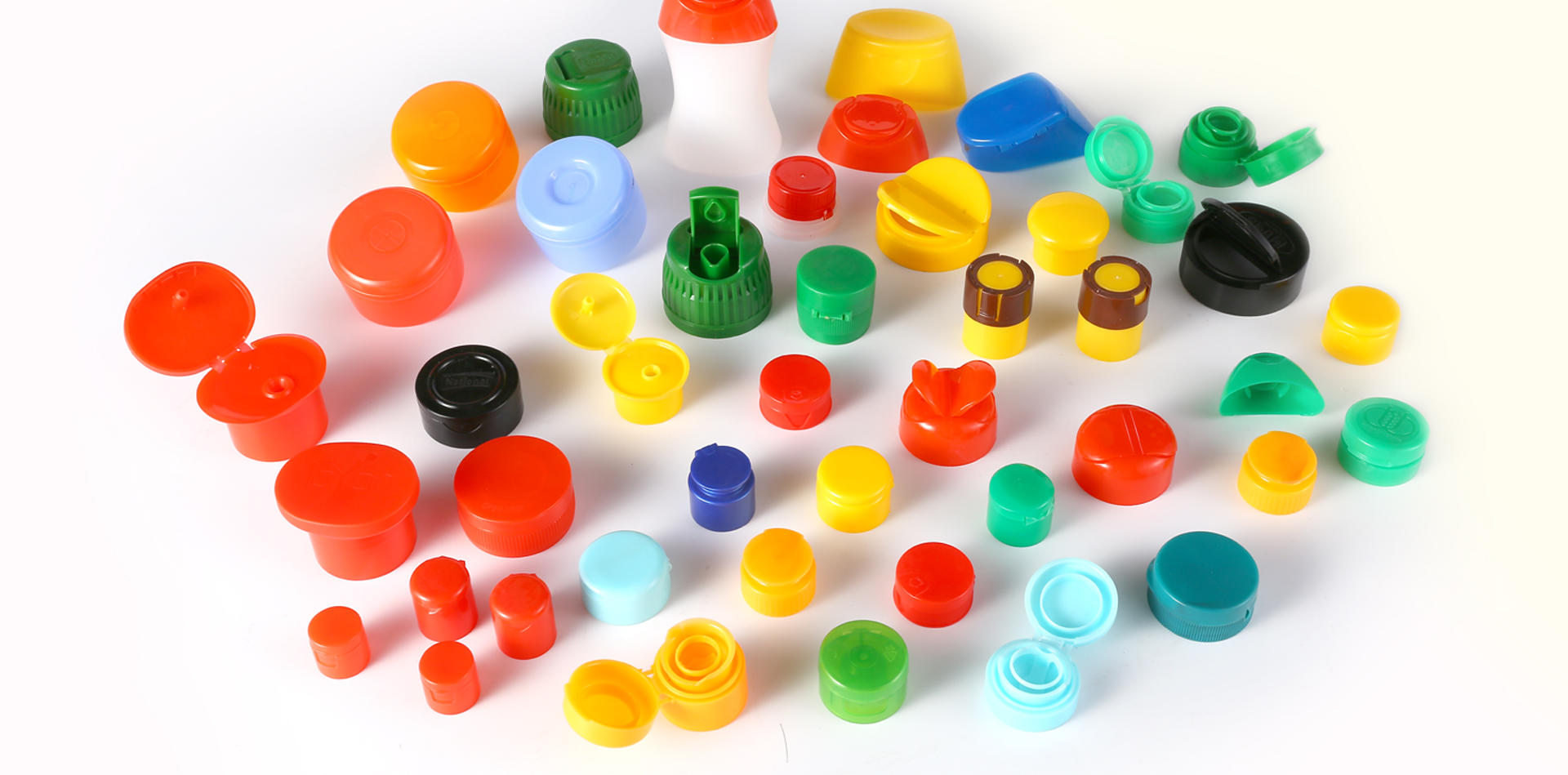
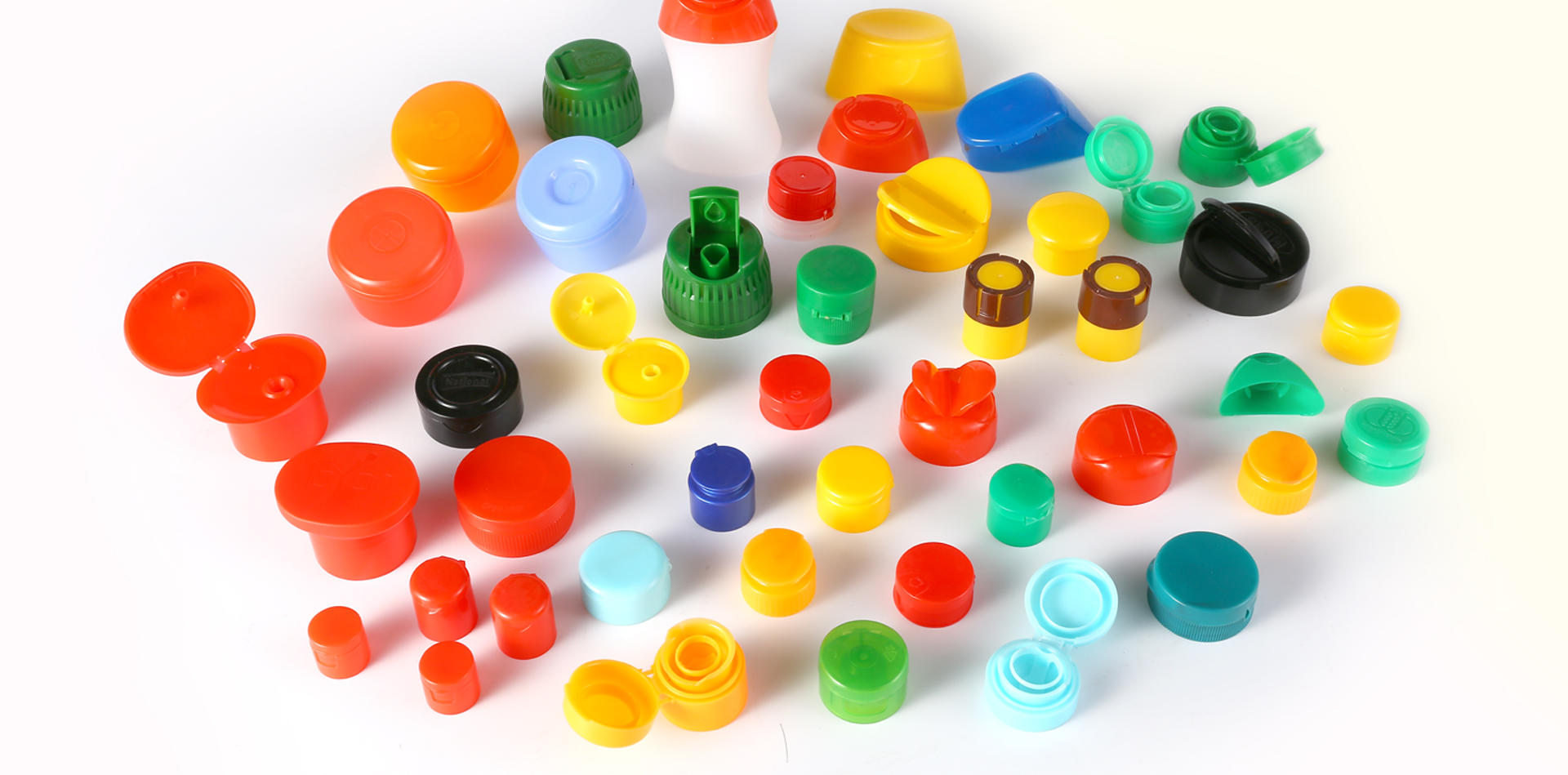
In summary, ensuring precision with 5 gallon cap moulds requires attention to detail throughout the entire process, from design and material selection to testing, maintenance, and process control. Quality assurance measures, including meticulous mould design and manufacturing, material selection, testing and validation, regular maintenance and calibration, process control, and continuous improvement, all contribute to achieving the desired precision and producing high-quality caps consistently.