Medical cap moulds are designed to create caps that provide a secure seal, preventing contamination of medical products. The moulds are constructed with materials that are resistant to microbial growth and easy to clean, minimizing the risk of contamination during the manufacturing process. Properly sealed caps help maintain the sterility and integrity of medical products, ensuring patient safety.
Engineered with precision to produce caps that have consistent dimensions, shape, and functionality. This precision ensures that each cap fits securely and performs reliably. Consistency in cap production is critical for maintaining quality control and ensuring that healthcare professionals can rely on the caps for safe and effective use.
High-quality medical cap moulds have a long lifespan and can withstand repeated use without significant wear or deterioration. Their durability ensures prolonged production efficiency and cost savings by reducing the need for frequent mould replacements. Investing in durable moulds pays off in the long run, as they provide reliable performance and reduce maintenance and replacement costs.
Medical cap moulds optimize material usage, resulting in cost savings. The moulds are designed to minimize material waste during the injection moulding process. They ensure that each cap is formed precisely and uses the required amount of material, minimizing excess and reducing material costs. This efficiency in material usage contributes to cost savings over time.
Precision and consistency are crucial in medical cap moulds to ensure the reliability and performance of the caps. The moulds should be designed with precise cavities and features to achieve accurate cap dimensions and specifications. Consistency in the moulding process is essential to produce caps with uniform quality and functionality.
Medical cap moulds are designed for ease of maintenance, which minimizes downtime and maximizes productivity. Regular cleaning and proper maintenance practices ensure optimal performance and prolong the lifespan of the moulds. Quick and efficient maintenance procedures allow for smooth production processes and reduce the risk of unexpected production interruptions.
Regular and proactive mould maintenance is crucial for preventing unexpected downtime and maintaining optimal production efficiency. Establish a preventive maintenance program that includes scheduled cleaning, inspection, and lubrication of the moulds. Address any issues promptly to minimize the risk of mould damage or performance degradation.
It is important to note that the use of medical cap moulds requires expertise in their operation and maintenance. Manufacturers should ensure that their staff is properly trained in handling and maintaining the moulds to maximize their efficiency and longevity.
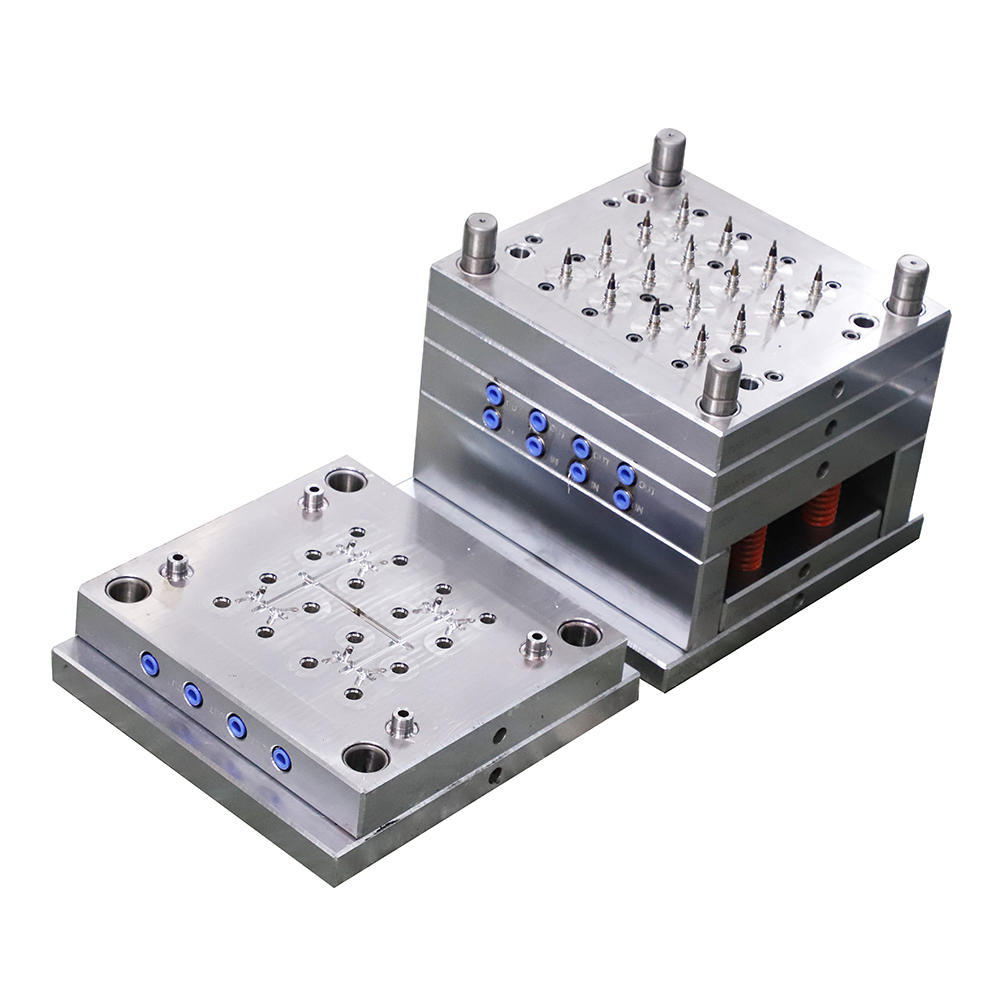
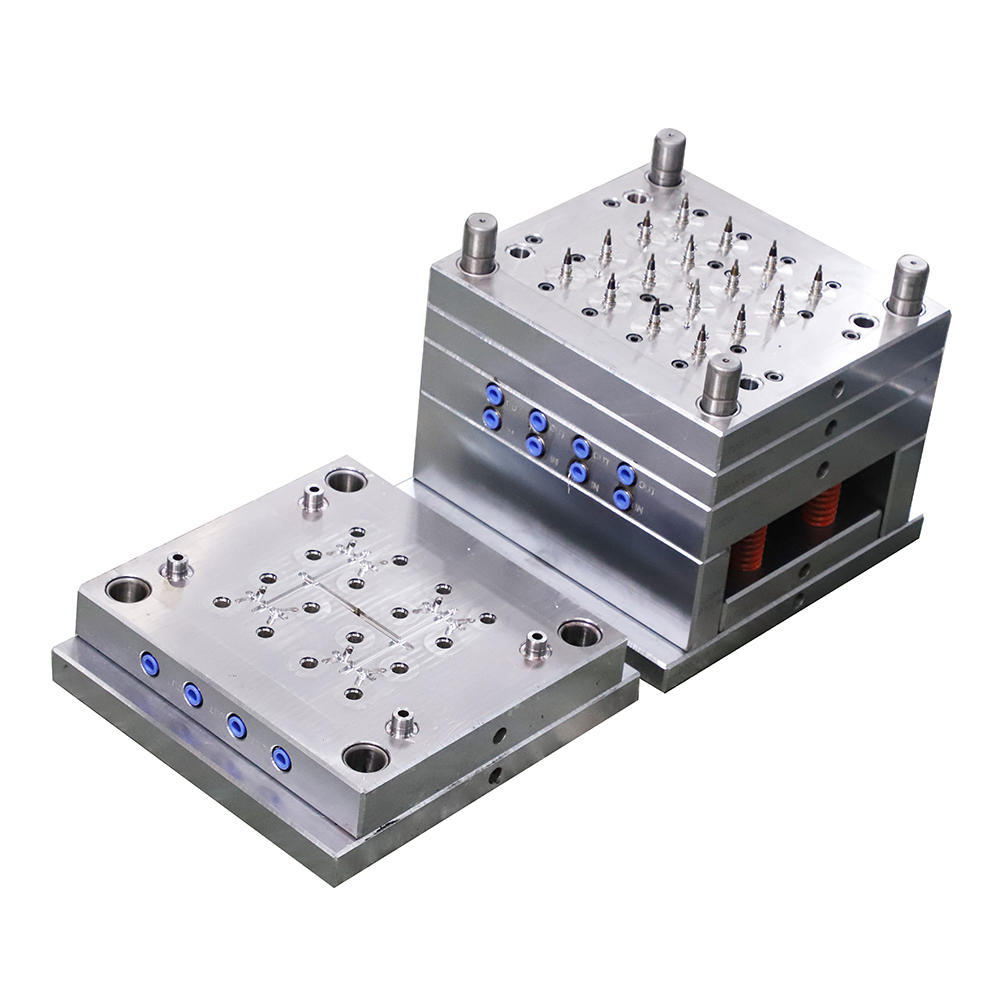
In summary, medical cap moulds offer significant advantages in terms of precision, production efficiency, cost savings, quality assurance, flexibility, ease of maintenance, and regulatory compliance. By investing in high-quality moulds and adopting efficient manufacturing practices, medical cap manufacturers can streamline their production processes, meet industry demands, and deliver high-quality caps for medical applications.