Getting the best results from a
water bottle cap mould requires careful attention to detail. There are a few factors that you must consider, including the type of material the mould is made of, the type of injection or compression moulding used, the temperature the mould is heated to and the demulding mechanism.
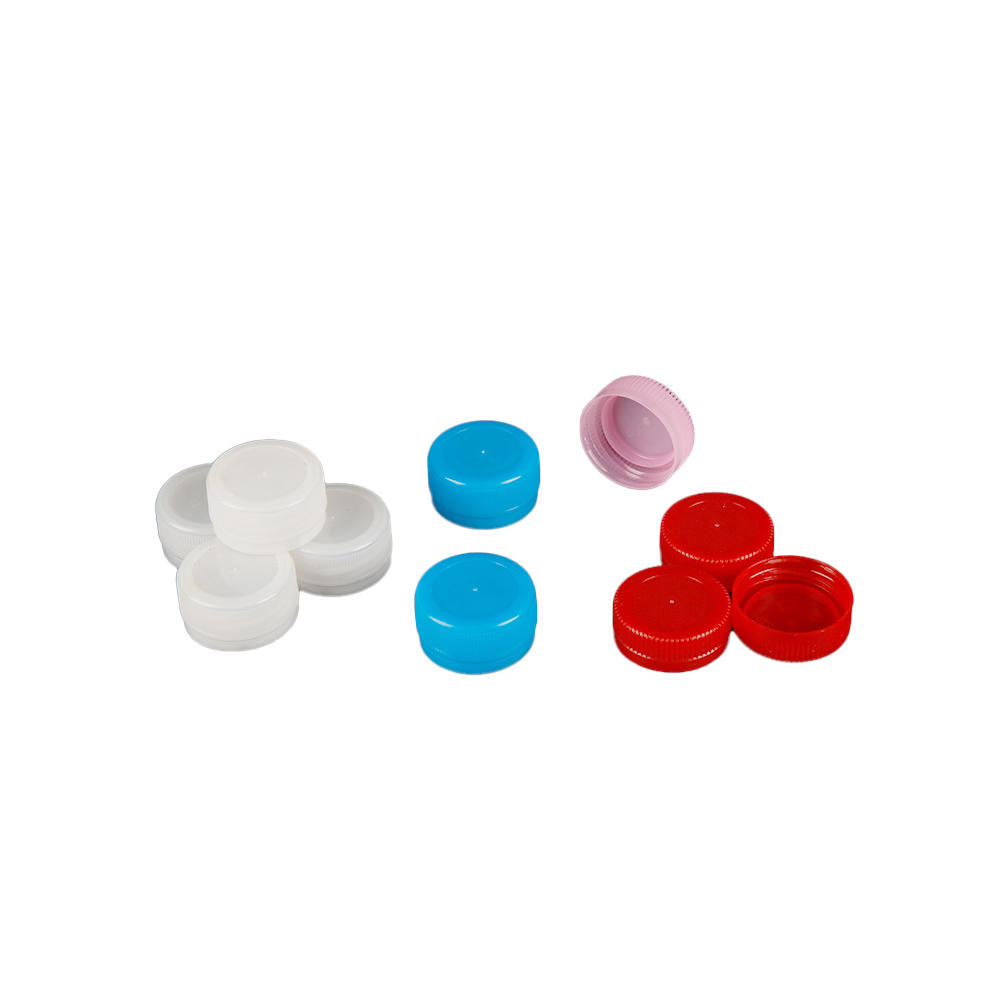
Several cooling techniques are available to cool the mold. The water temperature should match the surface temperature of the mold. This is because moisture can become trapped inside the mold if the coolant temperature is too low. The mold temperature is also important because it affects the quality of the lid product.
Injection molding is a common method for producing plastic bottles. The mold has multiple cavities that are injected with plastic pellets. The resin melts to form long, thin tubes. The pellets are then plasticized in the barrel of an injection molding machine.
Blow molding is another method for producing plastic bottles. The plastic pellets are melted by heat. The resin then flows through the RBM process.
A thermoplastic such as polyethylene or polypropylene is injected into a mold. After plasticizing, it is ready to fill. The plastic bottles are then trimmed to separate them from the mold.
Unlike injection molding, compression molding does not require a high molding temperature. This allows for reduced energy consumption.
Choosing the correct production method for making bottle caps involves a variety of factors. The choice is based on the volume, cost, shape, and design of the cap. It is also important to consider the quality of the bottle caps.
Injection moulding is one of the oldest plastic manufacturing processes. It uses the heat of conduction to melt plastic materials and then inject them into the mold cavity. This process allows for complex part geometry. It is a cost-effective technique that can be used for single-piece closures.
Compression moulding is an alternative plastic manufacturing method that uses pressure to shape the material. It is commonly claimed to be a cheaper alternative to injection moulding. This type of process offers good mechanical properties and durability. It is especially beneficial for high-volume productions. It has a reputation for being faster and easier to achieve color changes.
The most significant advantage of compression moulding is that the process is more energy efficient. This translates to less waste and lower costs.
Depending on what your product is made of, you may have a choice between foil wadded and polycell wadded water bottle caps. These are both fancy little gadgets that are made to keep your contents fresh. They are also designed to be recyclable, a win-win for your bottom line.
The Polycell Wadded Cap is a spongy pad that fills in the empty space at the top of a plastic or glass container. The spongy pad is accompanied by a foam component that ensures even foil contact during the packaging process. It is worth noting that the polycell was a bit of a mouthful.
A foil wad on the other hand is a polycell wad topped with foil. This allows for a great deal of flexibility in terms of the shape of the cap. It supports chemical compatibility and prevents spills. It also serves as a novelty and makes a neat display piece.